In the consumer electronics sector, aesthetics and functionality are inseparable. Devices such as smartphones, earbuds, smartwatches, and tablets rely heavily on sleek, precision-finished enclosures made from aluminum. Aluminum’s combination of low weight, excellent heat transfer, and good rigidity makes it a great material, but flawless finishes on CNC machined aluminum are not easy to achieve. Minor problems in the finishing process can either make the product less visually appealing or interfere with anodizing or assembly steps.
For best results, finishing a workpiece depends on selecting the most suitable tools, setting proper cutting and tool settings, and matching fixtures for holding and post-processing tasks. It covers real-life problems in machining aluminum for electronics and details how companies such as WayKen handle them using cutting-edge CNC approaches.
Contents
Surface Finish Expectations in Consumer Electronics
Brushes are provided only by hands, flat matte surfaces, and perfect anodizing cannot be skipped if you want the aluminum cases in consumer electronics look impressive. Slight imperfections such as a different machining mark, tool chatter, or burrs can still prevent the part from being accepted by the manufacturer.
In most cases, CNC machined aluminum surfaces that will be anodized must have an average surface roughness Ra falling between 0.4–0.8 μm. This can only be done when one keeps the machining conditions, prepping the part, and tool wear in check during each production run. Customers in the electronics sector often demand:
- Uniformity in texture across curved and flat areasUniformity in texture across curved and flat areas
- Clean, burr-free edges around ports and holes
- Surface profiles suitable for clear or color anodizing
- Fine detail resolution around buttons, logos, and interface features
When these expectations are combined with tight dimensional tolerances, the importance of process repeatability and material behavior under machining loads becomes even more critical.
Tooling and Parameter Challenges in Aluminum Machining
People often admire how aluminum can be machined, but CNC machining these grades of aluminum at very high speeds can create particular finish problems. The combination of aluminum being soft and building up edges in the cutting blade can result in tiny tears and irregular patterns on the surface of the material.
So, they have to get high-quality, sharp tools that have the best coatings. The chance of chips breaking can be lessened, and tool pressure more easily controlled with improved flutes and high angles (from 45° to 55°). While uncoated carbides are helpful for a brief run, ZrN and TiB2 coatings keep tools from sticking and help them last longer.
It is also important to choose the right cutting speed, stepover, and number of feeds. Spinning the fiber quickly at 18,000 to 30,000 RPMs can make the output smoother while also producing more heat. To prevent smearing or deforming the surface of printed boards due to heat, coolants must reach the chips, and the waste heat is removed. Even toolpath direction affects finish: A lot of the time, climb milling is used over conventional milling, as it reduces tool deflection and provides better surface finish.
Fixturing and Vibration: Underrated but Crucial
Problems with vibration caused by fixturing are a significant factor in why CNC machined aluminum parts sometimes finish badly. If not adequately supported, smartphone cases and wearable electronics made from thin-walled materials are likely to deflect and chatter.
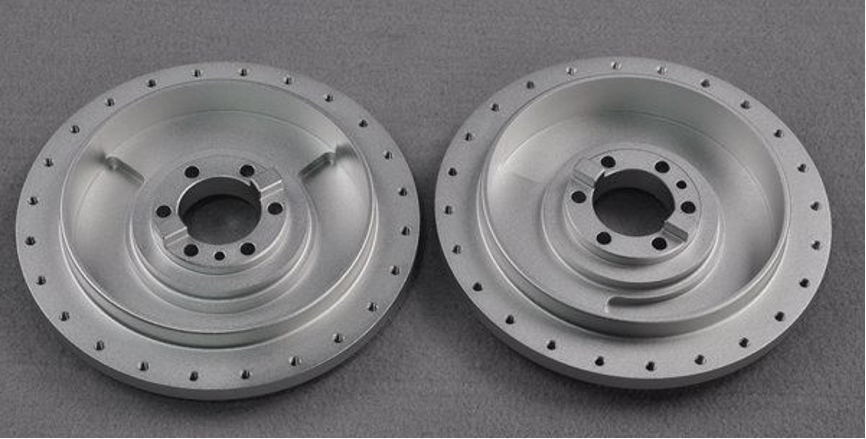
Machinists often depend on vacuum fixtures or custom soft jaws to ensure all parts of the piece are touching the cutting tool and to minimize the possibility of vibration during milling. When machining a part with several sides, how the part is placed must be planned to keep unsupported sections to a minimum at each operation.
With dynamic work holding, the part is automatically rotated, making it less likely for alignment errors to happen. Regular use of in-process probing systems increases the precision, as it allows for the proper alignment of pieces, which ensures equal quality on all faces.
Furthermore, using the same grip force and proper fixture hygiene are important, yet they are often left aside. If chips are left or if the surfaces of the piece are not perfectly level, marks in the finish may appear and require the part to be redone or thrown away altogether.
Post-Machining Treatments and Integration with Finishing Processes
CNC turning or milling may not be the only way to process a part. Consumer electronics items may require post-machining jobs such as deburring, vibratory finishing, bead blasting, or brushing to achieve their required surface quality. It is challenging to maintain the right dimensions in the product while still satisfying the required texture. For example, even though a bead-blasted surface is perfectly matte, the blasting can cause slight changes in the surface that could make gaskets or alignment problems arise. Overdoing the deburring process can remove the sharp edges, hindering the fit between two parts.
CNC machined aluminum is made using tighter tolerances because grinding and polishing will cause some material to come off. By following this process, the final piece ensures both its looks and mechanics are accurate without any corrections. In addition, checking the part’s finish with profilometry or visual method, directed by controlled lighting, ensures that uniformity is achieved for all batches and that requirements are met.
Advanced Strategies for Surface Optimization
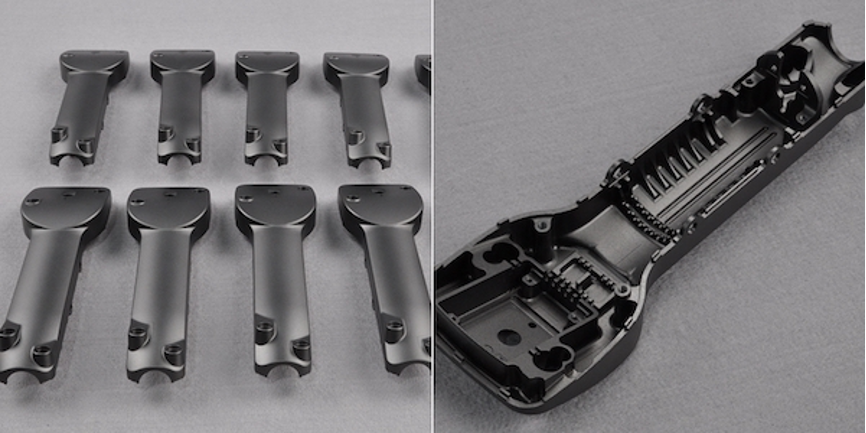
When there are more demands for machining, the technology must also rise in complexity. Surface smoothing settings in current CNC machines include planning paths ahead, low-pass filtering, and vibration damping on the go. Since even tiny marks on aluminum can influence both its function and how it looks, these capabilities are necessary for maintaining the finishing look of CNC machined aluminum.
There is also the option of planning toolpaths with scallop height control and pencil finishing around fillets. They minimize small steps and produce finer and better surfaces. High-speed machining that uses one chip at a time is also contributing to faster fabrication. Using programs that manage toolpaths to keep the tool consistently in use protects the surface and prevents it from being spoiled. The combination of coolant and high-pressure air eliminates debris from the surface, posing less risk for impurities in the USB-C port areas.
Conclusion
Surface finish quality is critical for CNC machined aluminum parts in consumer electronics, where visual perfection and tight tolerances are just as important as functionality. Every element—from toolpath strategy and cutting parameters to fixturing and post-processing—impacts the final cosmetic result. Trusted partners like WayKen ensure consistent, high-quality finishes by tightly controlling machining conditions and addressing aluminum’s unique surface behavior.